
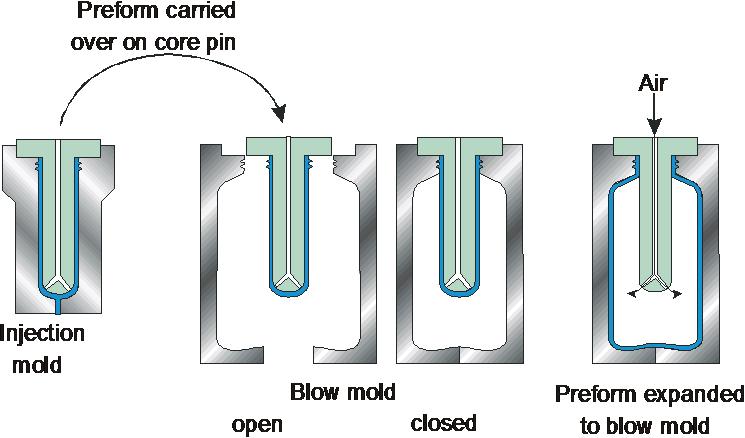
Natural balance means that the path of the melt to each cavity has the same length and number of turns. Most hot runners are also not naturally balanced. A variety of measures have been employed over the years with varying success. While PET is very good at self-leveling (the strain-hardening effect that compels initially warmer areas to blow out after cooler areas have blown), this effect is not significant enough to mask the uneven preform heat. If you were to stand in front of the machine you might notice that finished bottles are often thinner at the back because they were blown with warmer material in the back panel. When it is then divided into two streams (left and right, typically), warmer material flows to the back of the new channel. As the melt moves through the barrel and hot-runner channels it heats up unevenly. The uneven wall distribution is a result of viscous heating of the melt. This saves blow cavities and thereby reduces tooling costs, a critical issue for small- and medium-volume applications. These machines feature a multiple of two or three injection cavities per blow cavity, and the blow sections of the cycle two or three times for every injection cycle. The latter issue has led to a subcategory of single-stage machines that I call integrated two-stage machines. Inefficient blow station as the injection station always has precedence over the cycle time.The longer learning curve for operators, as two processes and PET drying must be mastered.Need to run machines run 24 hr/day to avoid higher scrap percentage.Quality problems with thermal-gated hot runners (valve gates are available and recommended).However, there are some disadvantages as well, including: In my view, these advantages make this process a no-brainer for all non-beverage containers. Thread start can be chosen to coincide with bottle shape.Good conditioning possibilities for oblong bottles on some machines.Both processes have their distinct advantages and disadvantages, and bottle producers and brand owners would be well advised to know those in order to make the right choice for their products. Both operations can be combined in one machine (the single-stage process) or in two (the two-stage process). Production of PET containers requires injection molding of preforms and subsequent stretching and blowing of these into bottles.
